Flexo or, flexographic printing is rated among the popular package printing methods, especially for medium to long term sustainable packaging. However, with several consumers going for business with brands that include eco-friendly strategies into their corporate model, it can pay well. You can be more intentional regarding your sustainable packaging efforts, mostly when you talk about flexo printing.
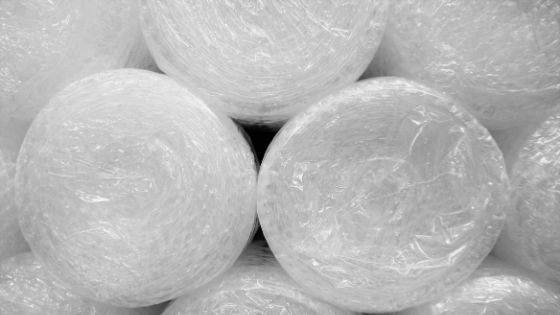
In this blog, we will take a bird’s eye view at sustainable product packaging. Also how high speed Flexo printer slotter die cutter stacker can boost any brand’s environmental strategy. Here’s a gander at the part that flexo plays in different sustainable packaging examples:
Sustainable Packaging Materials for Flexo Printing
Every experienced flexo printer understands there are four primary components to a fine print job. Those include:
- Substrates
- Inks
- Image carriers & anilox rollers
- Adhesives and Coatings
While these parts are critical for the process of flexo printing, there are methods to enforce their sustainability; regarding your wallet and the environment.
Substrates
Searching for sustainable packaging materials? If we talk about substrates, there are a plethora of options to pick from these days:
- Bioplastics
- Recycled plastics
- Sustainable recycled paper packaging
- Biodegradable and Compostable materials
Don’t worry about particular plastic films, as the quantity can go for recycle at store drop-off locations.
Spending some time in the design stage is worth it. You may discover various sustainable substrate options as per your packaging.
Caveat: Make sure the materials you are using has the approval for the product to be bundled up. For example, if you have to package anything consumable, you need to specifically research the most sustainable stuff for food packaging.
Other products might have less-rigid standards. Sustainability is essential, but ensure the substrate also reflects the product.
Inks
Without ink, you can’t have a print. Better ink choice is the first step towards a sustainable flexo printing practice.
It would be best to stay away from solvent-based inks. These inks tend to contain volatile organic compounds or VOCs. These chemicals are harmful and need extra precautions in the pressroom that suggests extra costs.
Some inks have cured with electron beams or ultraviolet light. These techniques are not as popular as water-based ink; however, for flexo printers that require a solvent-less system, hybrid inks are the way to go.
Hybrid inks make a combination of water-based inks’ convenience along with the resistance and bright shine of curable inks. Developing a system through an electron beam is costly, and maybe a long-term goal.
Changing inks might require some reworking of your flexo process as not all carriers of an image are suited for water-based inks. In the end, the amount reduction of harmful chemicals present in the air and water is worth the redesign.
Image Carriers & Anilox Rollers
Which image carrier you use? Photopolymer?
Do you have an idea that photopolymer plates can be reused and recycled in other plastic stuff? This is a fantastic way to cut down or save cost for brand-new equipment.
Moreover, photopolymer plates are not the bee’s knees with regards to eco-friendliness. Trace amounts of lead, mercury, and other harmful elements are in plates. Most of the times, these chemicals go down the drain when exposing the plate.
Submerging a sub-micro mesh filter into the disposal system of wastewater will go a long way for reducing the environmental effect from photopolymer plates.
Anilox Rollers
Anilox rollers are necessary to ensure an even ink spread on your image carrier. Also, often they are made of ceramic coating and steel. There are not several options regarding eco-friendly anilox rollers; however, that doesn’t mean there’s nothing you can do!
Rollers consistently come out of contact with ink; therefore, it is crucial to clean the rollers, right? How you wash/clean your anilox rollers defines how you can make a more environmentally conscious decision.
Common practices for cleaning involve harmful chemicals that liberate volatile organic compounds (VOCs) and need filtering systems and extensive capturing.
However, there are some ways to clean anilox rollers for a flexo printing job that pose little to no environmental impact. Take examples of water-based chemical cleaning or laser cleaning.
Elastomer Sleeves
Elastomer sleeve is an eco-friendly alternative to photopolymer plates. Elastomer sleeves are designed with a high-quality rubber for lasting print runs. Further, elastomer sleeves make sure a quality print job, no wasteful second run is necessary.
Sustainability is not just ensuring the usage of eco-friendly inks, substrates, and more. It is also about ensuring the flexo printing equipment is reaching its full potential. Elastomer sleeves keep flexo presses running better for longer and also being:
- Long-lasting
- Easy and fast to clean
- Highly detailed
- Simple to install
Adhesives and Coatings
Inks are only one component of “greening” your process of flexo printing. You would also need to ensure that you are using sustainable adhesives and coatings.
Typically, synthetic coatings or adhesives emit more VOCs. Therefore, sustainable designers move towards more renewable adhesive derivatives.
For instance, casein and gluten are effective adhesives. However, animal proteins are their source, so people avoid using them. The most sustainable and efficient adhesives are made using plant proteins, like corn starch or potato. Envelopes use adhesives (reactive) on the flap, where potato starch is activated by liquid; making it sticky.
Moreover, consider how recyclable your adhesives are. Whether or not they will break down without using harmful chemicals?
Last Word
Sustainability is now a go-to aspect in the corporate world. Sustainability has now become an increasingly concerning topic when we talk about flexo printing. To grab and remain on top of this trend will keep any pressroom eco-friendly and safe.